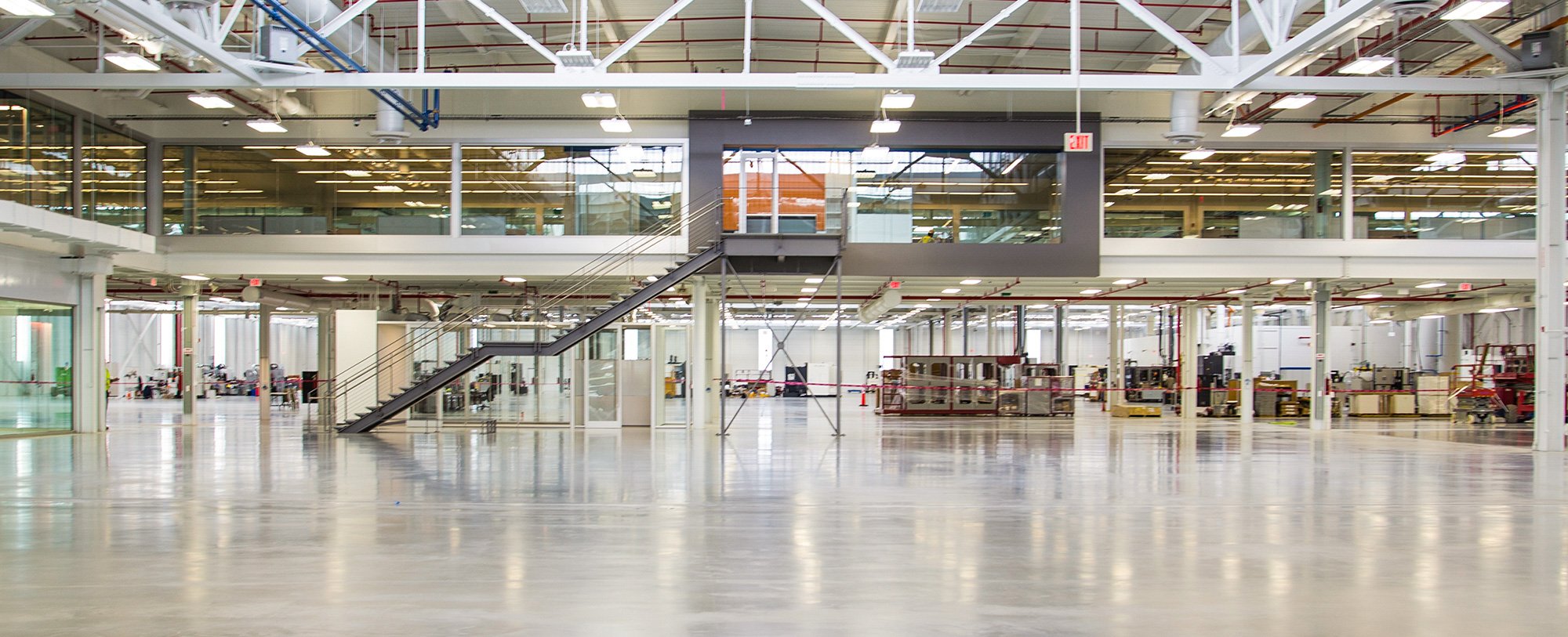
FAQ
Articles and Education
Specifying Steel Fibers for Concrete Floors - Construction Specifier, May 2014 (PDF)
An in depth and informative discussion on key factors and considerations for specifiers when working with fiber reinforced concrete floor designs. Includes essential features every steel fiber specification should cover.
-
Steel fiber reinforced concrete (SFRC) is a composite material made of hydraulic cements, water, fine and coarse aggregate, and a dispersion of discontinuous small steel fibers. It may also contain pozzolans and admixtures commonly used with conventional concrete. All admixtures meeting ASTM specifications for use in concrete are suitable for use in SFRC. Calcium chloride and chlorides from other sources should be limited to amounts permitted to be added to conventional structural concrete as shown in ACI 318.
-
Unlike welded wire reinforcement or rebar, which is specifically located in a single plane, steel fibers are distributed uniformly throughout the concrete matrix. The primary function of steel fibers is to modify micro and macro cracking, while WWR and rebar are designed to bridge cracks once they appear. Steel fibers are used to control cracking so that the composite will behave in a manner that we want rather than what conventional reinforcement allows. Steel fibers go to where the cracks originate while, conventional reinforcement lets the cracks grow until they reach the reinforcement.
-
WRI states in Tech Fact 705 that two of the primary purposes for reinforcing slabs-on-ground are for shrinkage and temperature control. Positioning is important when using WWR or rebar. WRI states that when one layer of reinforcement is used, it should not be allowed to be below mid-depth. In general, positioning at 1/3 the depth below the surface is sufficient. This is extremely difficult and requires the addition of chairs or slab bolsters to hold the reinforcement in position, an additional cost in material and labor. This problem is eliminated with the use of SFRC since the fibers are randomly distributed throughout the concrete. ASTM C1581 restrained ring testing also bears out the fact that steel fibers are very effective reducing crack width openings.
-
Wire-guided vehicles follow a cable embedded into the floor. For embedded steel to affect the wire guidance, the mass of steel must be substantial and it must lie very close (almost touching) the wire. Small, randomly distributed steel fibers do not meet the conditions that would cause trouble for the wire guidance. Steel fibers have been used successfully on many of the very narrow aisle applications.
-
Steel fibers can be introduced into the concrete at the batch plant or job-site. Consult ACI 544.3R or CFS’s brochure titled Mixing, Placing and Finishing SFRC for more details on the proper methods of adding fibers to concrete.
-
When fibers were first introduced to the market, balling was an issue due to the high aspect ratio and long length. Our standard fibers have aspect ratios of less than 50 and are either 1” or 1 1/2” in length. As the aspect ratio increase above 50 or the length exceeds 1 1/2”, the tendency of fibers to ball increases. This is the reason some of our competitors must collate their fibers to reduce the chances of fiber balls.
-
Pumping has been used to transport SFRC on many projects. In general, a mixture that will pump satisfactorily without fibers will pump with fibers. In pumping SFRC, the chute from the ready-mix truck should be 12” above the grate on the hopper of the pump. This will prevent the fiber from bridging the gaps in the grate and ensure a steady flow of concrete to the pump. The grate should never be removed from the hopper.
-
While there is always a chance of a fiber being on the surface of the slab, following the finishing techniques discussed in ACI 544.3R will keep them to a minimum. CFS’s fibers are designed to be the best finishing fibers on the market. To quote TR-63, “While high-quality surfaces can be achieved with any fiber type, small slit sheet steel fibers tend to be easier to finish.” In fact, many of our competitors recommend that a shake-on hardener should be used as a fiber suppressor to hide fibers which are on the surface of the slab.
-
No. If you use CFS steel fibers, and if the concrete mix is designed so that it would have good workability without fibers, you should expect no unusual difficulties in placing and finishing.
-
Laser Screeds and steel fibers are an ideal combination for today’s floors. The LaserScreed improves the floor flatness and increases productivity while the steel fibers improve the performance of the slab. Another advantage is that the steel fiber reinforcing is included in the concrete mix and does not impede the movement of the LaserScreed. This is not true with conventional reinforcement as it must be “chaired” in position before the concrete is deposited on the subgrade. This decreases the mobility of the Laser Screed and makes it almost impossible to get the mesh in the proper position.
-
Contraction joints can be installed using either a wet saw or early entry saw. For wet saws on slabs with a depth of less than 6″, the depth should be ¼ the depth of the slab. For slabs over 6” or slabs with over 50 pounds of steel fiber per cubic yard of concrete, the saw cuts should be 1/3 the depth
For early entry saws, manufacturer’s recommendations should be followed.
When making saw cuts, you should saw a 5’ length and make sure there is no spalling associated with the saw cut. If spalling is visible, the installer should wait 20 to 30 minutes and attempt the operation again.
-
No. The steel fibers we produce and recommend are used regularly without any dry shake.
-
No. Because steel fibers differ fundamentally from synthetic fibers, they cannot be considered equivalent. This is true whether the fibers being proposed are microsynthetic or macrosynthetic. While it may be possible to build a good floor with synthetic fibers, you cannot substitute them for steel fibers and expect the same performance.
-
Not without risk. The design recommendations endorsed by CFS are based on the use of CFS Type 2 fibers, 1-inch long. Other steel fiber types and lengths could be less effective in controlling and preventing cracks. Other types could also make the concrete harder to place and finish, and might result in more visible fibers at the floor surface.